Understanding Porosity in Welding: Discovering Reasons, Impacts, and Prevention Methods
Porosity in welding is a relentless challenge that can substantially affect the top quality and integrity of welds. As professionals in the welding industry are well conscious, recognizing the causes, impacts, and avoidance techniques associated to porosity is vital for accomplishing robust and trustworthy welds. By diving into the origin of porosity, analyzing its damaging impacts on weld quality, and discovering reliable avoidance methods, welders can enhance their expertise and abilities to produce premium welds continually. The elaborate interaction of elements adding to porosity calls for a detailed understanding and a positive method to guarantee successful welding results.
Common Sources Of Porosity
Porosity in welding is mostly created by a mix of variables such as contamination, incorrect protecting, and poor gas coverage during the welding procedure. Contamination, in the kind of dirt, oil, or corrosion on the welding surface, creates gas pockets when heated, leading to porosity in the weld. Improper shielding happens when the securing gas, generally used in procedures like MIG and TIG welding, is incapable to totally safeguard the liquified weld swimming pool from responding with the bordering air, causing gas entrapment and succeeding porosity. Furthermore, poor gas coverage, usually due to incorrect circulation prices or nozzle positioning, can leave components of the weld unsafe, enabling porosity to form. These variables collectively add to the formation of gaps within the weld, deteriorating its stability and possibly triggering structural problems. Comprehending and addressing these typical reasons are critical steps in stopping porosity and guaranteeing the high quality and toughness of bonded joints.
Results on Weld Top Quality
The existence of porosity in a weld can substantially jeopardize the total top quality and honesty of the bonded joint. Porosity within a weld creates gaps or cavities that deteriorate the framework, making it a lot more susceptible to cracking, rust, and mechanical failure. These gaps function as stress and anxiety concentrators, minimizing the load-bearing ability of the weld and raising the possibility of early failure under applied stress. Additionally, porosity can also serve as prospective websites for hydrogen entrapment, further exacerbating the degradation of the weld's mechanical homes.
In addition, porosity can hinder the efficiency of non-destructive testing (NDT) methods, making it testing to discover various other flaws or interruptions within the weld. This can result in considerable safety problems, especially in important applications where the structural honesty of the welded parts is critical.

Avoidance Techniques Overview
Offered the destructive effect of porosity on weld quality, effective prevention techniques are important to preserving the architectural honesty of bonded joints. In addition, selecting the suitable welding parameters, such as voltage, current, Discover More and travel rate, can help lessen the threat of porosity development. By incorporating these prevention strategies into welding practices, the occurrence of porosity can be significantly reduced, leading to stronger and a lot more trustworthy bonded joints.
Importance of Proper Protecting
Correct protecting in welding plays a crucial function in protecting against climatic contamination and making certain the integrity of bonded joints. Securing gases, such as argon, helium, or a mix of both, are frequently made use of to safeguard the weld swimming pool from reacting with elements in the air like oxygen and nitrogen. When these reactive elements come right into call with the warm weld swimming pool, they can trigger porosity, bring about weak welds with minimized mechanical residential properties.

Poor shielding can lead to different defects like porosity, spatter, and oxidation, compromising the architectural stability of the bonded joint. Sticking to correct shielding practices is vital to produce high-quality welds with minimal defects and ensure the long life and reliability of the bonded elements.
Monitoring and Control Approaches
Exactly how can welders effectively monitor and control the welding procedure to guarantee ideal outcomes and prevent problems like porosity? One trick technique is via making use of innovative monitoring innovations. These can consist of real-time surveillance systems that give feedback on specifications such as voltage, present, take a trip speed, and gas circulation prices. By constantly monitoring these variables, welders can determine discrepancies from the optimal problems and make instant changes to avoid porosity formation.

Furthermore, carrying out proper useful link training programs for welders is find vital for checking and managing the welding procedure properly. What is Porosity. Enlightening welders on the relevance of preserving constant criteria, such as proper gas securing and take a trip speed, can aid prevent porosity issues. Normal evaluations and accreditations can likewise make certain that welders excel in tracking and regulating welding procedures
Moreover, the use of automated welding systems can boost monitoring and control capabilities. These systems can precisely control welding criteria, reducing the likelihood of human mistake and making sure consistent weld top quality. By incorporating innovative monitoring modern technologies, training programs, and automated systems, welders can efficiently keep track of and control the welding process to decrease porosity issues and attain premium welds.
Verdict
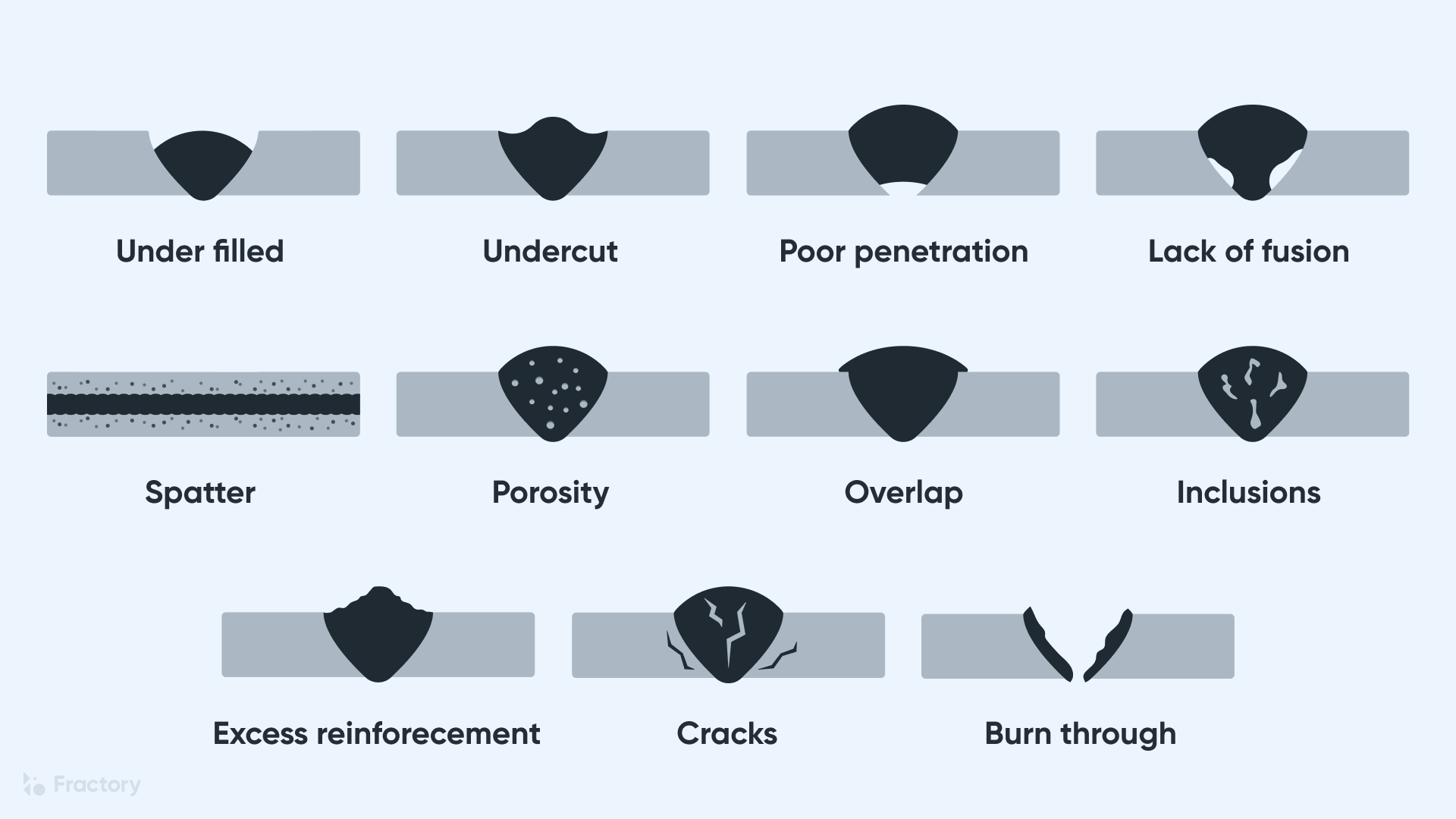